Operations Management
Employee Utilization
Written by Andrew Goldman for Gaebler Ventures
Switch your company focus to keeping your employees busy instead of your machines. Maximum machine utilization leads to overproduction and added costs while maximum employee utilization leads to cost savings and a stronger workforce.
A traditional approach to Operations Management revolved around keeping the machines busy.
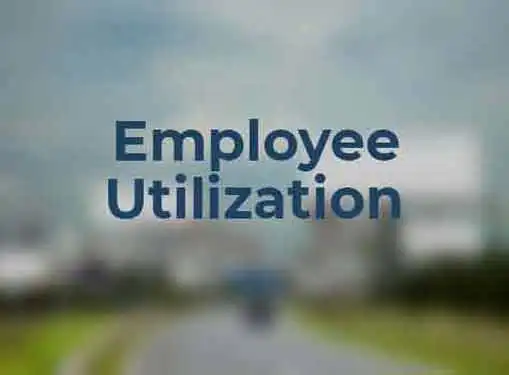
The idea was that equipment was expensive and should be fully utilized. Accountants encouraged this as well, believing the more the machine was running, the more the cost of the machine could be absorbed.
As Operations Management has evolved, so has this line of thinking. Instead of running machines for the sake of keeping them running, we want to keep our employees busy and maximize our employee output.
You want to make sure that you are producing what it is demanded. When you keep a machine running, just to keep it running, you're not producing to meet demand requirements. If you're overproducing, you're not really saving money, you're adding costs.
Overproduction leads to excess inventory, which is not an ideal situation. Excess inventory can be extremely costly due to material handling, the risk of damage and the most expense risk of obsolescence. If you're building inventory to meet expected demand, which is a different story.
When your focus is on keeping machines busy, you're greatly underutilizing one of your most valuable assets; your employees. Employees are encouraged to watch machines and stock inventory, two non-value added activities. If we switch our focus to ensuring that our employees are kept busy instead of our machines, we can greatly improve our operation. Instead of watching a machine produce added inventory, we can use our employees to improve our processes, quality control and efficiency.
A great example of this is a fast food restaurant. If an employee is focused on operating the French fry machine all day everyday he/she is being underutilized. There may be time when French fries aren't demanded.
During these times, the fry operator should help in other areas of the kitchen or work on cleaning the work area. If his focus is solely on producing French fries, other areas of the kitchen will suffer when French fries are not in demand.
This may be a simple example but illustrates a very important point. There are times when an employee could be better utilized in other areas of our operation, but we have them stuck operating a machine and producing unnecessary product. Employees should also be cross-trained in as many areas as possible. By cross-training our employees we improve flexibility and responsiveness. Time spent watching machines could be spent cross-training our employees and drastically improving our workforce.
In general, you want to balance your flow of work so actual demand is being met. Don't fall into the trap of running machines to keep your employees busy. If this is your strategy you'll wind up overproducing and underutilizing your employees.
There's always something to get done and you should feel comfortable shuffling your employees around to best meet your company's needs. Employee satisfaction will increase as their responsibilities do the same.
Your employees will be thankful that they can experience other aspects of your operation besides watching machines operate.
Andrew Goldman is an Isenberg School of Management MBA student at the University of Massachusetts Amherst. He has extensive experience working with small businesses on a consulting basis.
Share this article
Additional Resources for Entrepreneurs
Conversation Board
Share your comments, questions and advice regarding employee utilization.